Flaw Detector External Scanning DNS 1000-1400
Structurally, the flaw detector is a detachable frame covering the pipe. In the upper part of the frame there is an autonomous power supply, a power shield, electric motors for rotating scanners, a longitudinal drive and steering engines, a longitudinal odometer, a vertical position control system, and a radio data transmission channel. Inspection of the pipe is carried out by two magnetic scanners mounted on a gear wheel rotating around the pipe. One of them magnetizes it in the longitudinal direction, and the other in the transverse direction. With this approach, the most complete identification of defects of various orientations is ensured. There is also an electronic unit.
Each scanner consists of a special configuration of the magnetic unit and the sensor unit. In the process of development and manufacturing, the optimal parameters of magnetic blocks were achieved, providing high intensity and uniformity of the magnetic field. The original telemetry scheme of electronic units with the transmission of digital information via a high-speed radio channel allows the operator to identify defects in real time and reduce the time of the final analysis of the defectogram of the next scanned pipe.
The power supply of the electronic unit and the sensor unit is made from accumulator batteries.
Uninterrupted power supply of the on-board network is provided by an alternator with remote start.
The longitudinal movement of the flaw detector and the movement of scanners around the circumference of the pipe is carried out on road wheels.
The complex includes highly informative diagnostic information analysis software with a flexible documentation system.
High reliability of the flaw detector is ensured by the use of certified components and assemblies, the use of advanced materials and manufacturing technologies, and developed software and hardware diagnostic tools.
Specifications
Parameter | Value |
---|---|
The level of the longitudinal and transverse magnetizing fields in the pipe with a thickness of 17 mm | 35-50 kA / m |
Non-uniformity of the magnetic field along the line of sensors during longitudinal and transverse magnetization | ± 0.5% |
Range of wall thicknesses of the controlled pipeline | 9 - 21 mm |
The limits of adjustment of the air gap between the magnetic system and the surface of the pipe | 2 - 15 mm |
The minimum depth of the detected defect size 30 * 30 mm | 0.05 t |
The minimum diameter of the detected defect at a depth of 0.3 t | 4 mm |
The error in determining the depth of the defect with a probability of 80% | 0.1 t |
Error in determining the length and width of a defect (general corrosion) | ± 10 mm |
Ultimate detection depth for longitudinal and transverse cracks ≥25 mm long and 0.1 mm wide | 0.05t |
Accuracy of determining the depth of cracks | 0.2 t |
Longitudinal speed | 1 - 2 m / min |
The flaw detector remains operable in the range of ambient temperatures from -30 to +50 degrees C with relative humidity and precipitation in the form of rain, snow, dew, hoarfrost.
The time for preparing the CSN for work by 2 specialists is 45 minutes (installation on the pipe body, assembly, tuning).
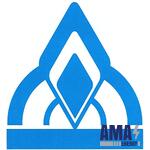