Separator
Scandinavian quality in every detail
Alfa Laval separators are most frequently used in the fleet. The inter-plate gap of this company's separators is reduced by 17-22% compared to other companies. Due to this, it was possible to increase the number of plates in the drum without increasing its dimensions. A distinctive design element of these models is the presence of specific pressure disks that serve as a replacement for traditional pumps for pumping out fuel and oil. The company pays great attention to the issues of automation of the separation process. For example, the Alfax and Alcap technologies developed by the company ensure the operation of Alfa Laval separators in automatic mode, performing all working operations according to a predetermined program. Emergency signaling and protection are also provided. The partial unloading method used in the new Alfa Laval separators has reduced fuel or oil losses, water consumption and maintenance costs. Alfa Laval is constantly improving its products. In the field of shipbuilding and ship repair, the company's new development is the separation systems of the S and P Flex series. The Alfa Laval separator type S complies with the requirements of CWA 15 375 (Standard on the Performance of Marine Separation Systems). It uses Alcap technology. The system parameters are adjusted automatically depending on the density of the heavy fuel oil. The Alfa Laval separator type P does not use Alcap technology. The gravity disc is manually selected depending on the density of the heavy fuel oil. This economical version is used for separating diesel fuel and lubricating oil of uniform density. Automation of control is carried out using the EPC 60 modular control unit, which has protection against vibration and high engine room temperatures.
With German precision especially for you
Another well-known representative of this class of machines is the westfalia separator. GEA Westfalia Separator supplies separation systems designed specifically for continuous operation in the harshest conditions. This provides you with:
• Optimal performance
• Long service life of your engines
• High environmental standards
Westfalia self-cleaning separators with UNITROL systems automatically monitor the water content of the oil product during 24-hour solids cleaning. This ensures optimum separation efficiency for different types of fuel and lubricating oils. Maintenance is generally only required after 8,000 to 16,000 operating hours. Unattended operation significantly simplifies the work of the engine room crew. The collected oil sludge can be processed on board, which significantly reduces waste disposal costs. All separation systems can be supplied as separate modules. The new westfalia "eagleclass" separator class was developed using the know-how of the technology leader in centrifugal separation processes. The innovative separator design and the new Westfalia Separator® unitrolplus control system set new standards in the market segments of energy, marine technology, oil production and refining, industry and environmental technology. High centrifugal forces made it possible to achieve a capacity of 80 m3/hour for the first time. The Westfalia Separator® unitrolplus system guarantees maximum separation efficiency for various liquids such as fuel, lubricating oil, oil-contaminated water, washing lye, etc.
Westfalia separators are time-tested and sea-tested units, ready to operate in the most difficult conditions.
In addition to supplying assembled separators, Norta MIT offers spare parts for separators, both new models and separators that have been in operation for quite some time. Send a request to our office by E-mail or directly from the website, and our managers will help you select the separator or spare parts for separators you need.
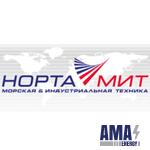