Stress Analysis: Simulations, FEM Analysis
We are using FEM to perform stress analysis on the product’s critical components with complex geometry to evaluate the feasibility of the design concept; to predict the performance and behavior of the design; to calculate the safety margin; and to identify the optimal design.
The simulation results with interpretation and conclusions can be presented for our clients in report form.
Stress analysis are not a substitution of experimental testing, but combined with Design Engineer experience, results in fewer prototypes and saving time and development costs.
This is how FEM works:
- 3D model is being broken down into thousands to hundreds of thousands of finite elements (f.ex. 4-noded tetrahedrals like in the picture on the side) forming a mesh
- Design Engineer defines input parameters: material properties; constraints that limits the component’s displacement; forces applied to the component during operation
- Simulation process is run based on the input parameters The results are plotted on the model using colors and line plots
- Design Engineer interprets the results to make the final decision
CAD programs run linear analysis calculating the stresses and deformations of geometry given three basic assumptions:
- The component under load deforms with small rotations and displacements
- The product loading is static and constant over time
- Material properties do not change
Stress analysis is an engineering discipline covering methods to determine the stresses and strains in materials and structures subjected to forces or loads.
Finite Element Analysis (FEA) is a computerized method for predicting how a real-world object will react to forces, vibration, heat, and etc. in terms of whether it will function as planned.
Safety Factor (safety margin) is a ratio of how much stronger the object is than it usually needs to be for an intended load.
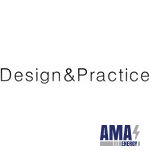