Flaw Detector Portable VID-345 Magnetic eddy Current
The device combines magnetic and eddy current methods for detecting defects , which ensures control of products with a rough, corroded surface and work through a layer of insulating coating of variable thickness without additional settings.
Objects controlled by VID-345:
- pipes, pipelines,
- oil and gas pipelines,
- vessels, pressure vessels,
- objects of energy production,
- details of structures, machines and mechanisms.
The VID-345 flaw detector passed metrological certification and was entered in the State registers of measuring instruments of the Russian Federation and the Republic of Kazakhstan.
Simultaneous detection and determination of the depth of stress-corrosion cracks, the thickness of the insulation coating and / or corrosion during the scanning process. Advantages of the device
- Detection of corrosive ulcers through continuous scanning of the thickness of the insulation coating.
- Operational adjustment of operating modes.
- Threshold adjustment for minimum detectable crack depth and thickness of insulation coating.
- Light, sound (included headphones) defect alarm.
Flaw detector design features
The metal casing of the electronic unit of the flaw detector can withstand harsh operating conditions in the field or production conditions.
The sensor housing is made of metal, the contact surface is made of high-strength ceramic, which ensures abrasion resistance.
- The intuitive Russian-language interface is organized on the principle of "INCLUDE AND WORK."
- Equipped with additional interchangeable sensors.
Specifications
Minimum crack depth | 0.2-0.5 mm |
Minimum crack opening | 0.05 mm |
Minimum crack length | 5 mm |
Crack Depth Range | 0.3 - 5 mm |
Fracture Depth Accuracy | 0.2 mm + 0.1h (where h is the depth) |
Range of determination of the thickness of the protective coating or the depth of corrosion damage | 0 - 6 mm |
The error in determining the thickness of the protective coating or depth of corrosion damage | 10 % |
Maximum insulation thickness for crack depth determination | 10 mm |
Operating temperature range | -15 ... + 40 ° С |
Flaw detector electronic unit dimensions | 150 x 80 x 35 mm |
Sizes of the regular sensor "N-345" | 25 x 25 x 60 mm |
Flaw detector electronic unit weight | no more than 500 g |
Power supply | Autonomous from 2 rechargeable batteries of the Ni-MH type (1.2 V) or similar, or from batteries of the type AA 1.5V ALK |
Continuous Battery Life | up to 10 hours |
Battery Discharge Control | there is |
Warranty period | 12 months |
Contents of delivery
Kit components | "Standard" | "Special" |
Flaw detector electronic unit | v | v |
Standard sensor "N-345" | 1 PC. | 2 pcs. |
Cable for connecting the sensor to the device | 1 PC. | 2 pcs. |
Control sample with simulated cracks 2 mm deep | v | v |
Control sample of an insulating coating 2 mm thick | v | v |
Battery (a set of 2 pcs is pre-installed in the device) | 1 kit | 2 pcs. |
Charger | v | v |
Headphones with an adapter | v | v |
Operation manual (combined with passport) | v | v |
Verification Certificate | v | v |
Protective cover with belt for fixing the device on the operator’s chest | v | v |
Cuff for fixing the device on the operator’s hand | v | v |
Bag for safe transportation and storage | v | |
Suitcase for safe transportation and storage | v | |
Specialized calibration and customization for customer tasks | v |
Additional accessories
- Additional interchangeable sensors.
- Cable for connecting sensors to the flaw detector.
- A set of spare batteries.
- Control samples.
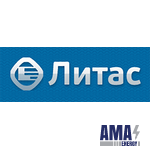