Lel-M / A-Line 32D (DDM-M)
The hardware Lel-M / A-Line 32D (DDM-M) / system is implemented as a distributed system for collecting and processing diagnostic data and consists of a central computer station (CVC), electrical isolation and power supply cubicle cabinets (KShGR), control and measurement modules and switching (MUIK), concentrators and a set of digital multifunctional measuring modules in explosion-proof execution (MSME).
The KDM Lel-M / A-Line 32D system (DDM-M) / is certified for compliance with the requirements of GOST R 51330.0-99 (IEC 60079-0-98), GOST R 51330.1-99 (IEC 60079-1-98), GOST R 51330.10-99 (IEC 60079-11-99), which regulates the use of electrical equipment in the hazardous area, and has an explosion protection mark 1Exd [ib] IIСТ6, or 1Exd [ib] IIВТ6, or 1Exd [ib] IIАТ6.
Based on the Lel-M / A-Line 32D (DDM-M) / system, various configuration options for monitoring systems designed to solve a wide range of tasks can be implemented.
Characteristics
Common parameters | |
Supply voltage of TsVS, KShGR, intermediate station (technological unit) | 220V / 50 Hz |
The maximum number of MSMEs in the KDM system | no more than 768 pcs. |
The maximum number of measuring channels in the KDM system | no more than 2304 pcs. |
Multifunctional Measurement Module (MSME) | |
Maximum number of simultaneously used channels | 6 pcs. * |
The composition of the channels of measurement, control, communication and switching:
| |
Type of data transmitted | digital self-synchronizing code |
Cable type | twisted pair |
Maximum cable length between adjacent IHR | 120 m |
Galvanic isolation | not worse than 500 V |
Operating temperature range | -40 ÷ +60 ° С |
Supply voltage | 48 V |
Power consumption | no more than 10 watts |
Weight | no more than 5 kg |
* - depends on the configuration of the IHR | |
Acoustic emission channel | |
Operating frequency range | 1 ÷ 1000 kHz (15 ÷ 500 kHz as standard) |
Signal Filtering: | |
| 18 dB / octave |
| 40 ÷ 60 dB / octave |
Frequency response in the operating frequency band | + 1 / -3 dB |
The maximum measured amplitude of the AE signal | 94 dB |
Signal amplitude accuracy | ± 1 dB |
Noise level brought to the input in the working frequency band | no more than 5 mkv |
Time accuracy | 1 Moscow time |
AE Signal Registration Speed | no less than 800 sob./channel |
Current loop measuring channel | |
Operating range of the measured current value | 4 ÷ 20 mA |
Measurement accuracy | 0.2% |
Voltage measuring channel | |
Maximum Input Voltage Range | ± 10 V (0 ÷ 5 V as standard) |
Input impedance | 10 kOhm |
Measurement accuracy | 0.5% + 0.1% of range |
Current loop control channel | |
Input current range | 0 ÷ 22 mA |
Maximum load resistance | 800 ohm |
Current Accuracy | 0.2% |
Bridge meter channel | |
Execution options for operating modes | ¼ bridge, ½ bridge, bridge |
Minimum shoulder resistance of the connected bridge | 120 ohm |
Relative error of measuring the unbalance of the bridge | 0.1% |
Expansion board | |
Types of Front Ends | RS232, RS485, RS422 |
The number of lines of external interfaces | no more than 3 |
The main elements of the system
- The Lel-M / A-Line 32D (DDM-M) / system consists of the same basic devices and has a common control core based on a central computer station.
- The central computing station provides the accumulation and complete analysis of all received data, their display, decision making and the formation of control commands for multifunctional measuring modules and executive equipment.
- Switch cabinet - a device designed to provide power and galvanic isolation of concentrators and measuring lines.
- KShGR carries out galvanic isolation between the primary voltage of 220V / 50Hz and secondary DC voltage of 48 V supplied to the cascading line of the IMSS, as well as optocoupler isolation in the data transmission channels.
- The control, measurement and switching module is designed to measure the analog signals coming from the sensors, generate analog control signals for external actuators and switch (switch) the measuring and executive circuits.
Structurally, the MUIK is a holder with a carrier (motherboard) board installed, in the slots of which channel cards are installed:
- KI - measuring channel of the current loop for recording slowly changing parameters from primary or secondary converters equipped with a current output of 4–20 mA;
- KU - control channel of the current loop for controlling various devices equipped with a current control input of 4–20 mA;
- KR - a switching channel that provides switching external circuits using relays according to a given algorithm.
The measuring line (MSMC cascading line) is a control, synchronization, data transmission and power supply channel that provides the connection of multifunctional measuring modules to a concentrator or KShGR.
A hub is an explosion-proof communication device that provides support for several measurement lines for connecting multifunctional measurement modules and is equipped with a high-speed digital communication channel (Ethernet) for communication with a central computer station.
Multifunctional measuring module - a device that provides galvanic isolation of measuring channels, receiving analog signals from diagnostic and parametric sensors, converting them into digital form and subsequent processing.
Each module can contain a combination of up to three any blocks of measurement or generation of control signals for executive equipment:
- AE - a channel for recording acoustic waves, the channel contains analog and digital frequency filters, an amplifier, an analog-to-digital converter, a digital amplitude comparator, computing devices for calculating the characteristics of AE signals;
- ITP - measuring channel of the current loop for recording slowly changing parameters from primary or secondary converters equipped with a current output of 4–20 mA;
- USP - the control channel of the current loop for controlling various devices equipped with a current control input of 4–20 mA;
- MI - channel of the bridge meter for measuring the deviation of the resistance in the shoulders of the resistive bridge sensor from the original value.
Sensors - primary converters of physical quantities into electrical signals
Acoustic Emission Converters (PAE)
They are used to register acoustic emission signals arising from plastic deformation of solid media, the development of defects (cracks, microcracks, delamination, corrosion, hydrogen embrittlement, etc.), friction, leakage (the passage of liquid and gaseous media through through defects).
Pressure transmitters
They are used to record the values of overpressure, rarefaction, overpressure-vacuum, absolute pressure, differential pressure and hydrostatic pressure (level) of liquid and gaseous, including aggressive media, in the studied control objects.
Strain gauges (strain gauges)
They are used to assess the stress-strain state of the structure.
Corrosion sensors
They are used to measure the corrosion rate by the method of electrical resistance (ER - electric resistance) or by the method of linear polarization (LPR - linear polarization resistance).
Vibration sensors (vibration velocity sensors with current output)
Designed to convert to DC direct mean square values of vibration velocity at controlled points of installations and equipment.
Temperature sensors (resistance thermometers, thermoelectric converters)
Designed to measure the temperature of liquid and gaseous media.
Temperature sensors (resistance thermometers, thermoelectric converters)
Designed to measure the temperature of the working surface of the control object.
Integrated diagnostic monitoring systems (CDM) are based on several non-destructive testing methods, providing timely detection of all types of structural and operational defects in controlled areas with high reliability.
Appointment
- Improving the operational safety of facilities, achieved by detecting changes in the technical condition in real time.
- Timely detection of damage accumulation sites, determination of their nature and degree of danger.
- Continuous monitoring (monitoring) of the technical condition of the objects during their operation based on various methods of non-destructive testing, stress-strain state, measuring the operating parameters of the process and tracking factors that affect the damage to the object.
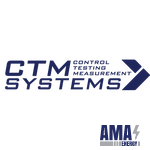