Vortex Electromagnetic flow Converters VEPS
Today, PromService JSC produces a vortex electromagnetic VEPS flow converter, starting from DN20 and ending with DN300, in several modifications, depending on the version of the UVS.
According to the type of output electrical signal, flow converters with non-normalized (frequency), normalized per volume unit (pulse) output, and also with a standardized current output of 4-20mA are produced. At the same time, depending on the diameter of the flowing part, the primary converters, while maintaining the main structural elements, are divided into designs of small (DN20-50), medium (DN80-150) and large diameters (DN200-300).
A significant advantage of VEPS is the relative simplicity of the design and, consequently, low cost, metrological characteristics sufficient for commercial accounting (error of not more than ± 1.5%, dynamic range - 32, intertesting interval of 4 years). When converting fluid flow, VEPS does not use the amplitude parameters of the measured signal, which in turn has a positive effect on the stability of its characteristics during operation.
Registered in the State register of measuring instruments of the Russian Federation under No. 14646-05.
The design of the VEPS transducers is protected by the patent for invention No. 2350911 “Vortex electromagnetic fluid meter sensor”.
Since 2007, the production of a VEPS modification with an upper magnetic system (VEPS VRM) has begun, which has the best performance characteristics compared to the old design:
- less susceptible to the deposition of ferromagnetic particles in the flow part of the device at the location of the magnet. At the same time, even those insignificant deposits of ferromagnetic particles that can accumulate at the place of installation of the magnets do not lead to a short circuit of the electrode on the housing and, accordingly, to the failure of the devices;
- metrological characteristics of VEPS with a new design of the magnetic system have not changed compared to the old design;
- the UFS housing rack is made of plastic, has lower thermal conductivity compared to steel, therefore, the UFS housing together with the electronic module is less susceptible to thermal heating, which improves the working conditions of the electronics.
Diameters of conditional pass (Du) VEPS: 20; 25; 32; 40; fifty; 80; one hundred; 150; 200; 250; 300 mm
Mm | The value of flow, m3 / h | ||
---|---|---|---|
Qmin | Qt | Qmax | |
twenty | 0.3 | 0.5 | 8 |
25 | 0.4 | 0.63 | 10 |
32 | 0.5 | 1,0 | sixteen |
40 | 0.8 | 1,6 | 14 |
fifty | 1,0 | 2.0 | 32 |
80 | 2.5 | 5,0 | 80 |
one hundred | 5,0 | 10 | 160 |
150 | 12.5 | 25 | 400 |
200 | 25 | 40 | 630 |
250 | 32 | 63 | 1000 |
300 | fifty | one hundred | 1600 |
VEPS converters have the following modifications:
- VEPS-PB1-01 - converts the value of the flow rate and volume into a pulsed electrical output signal with a frequency proportional to the flow rate, in accordance with the individual calibration characteristic. The signal frequency is equal to the vortex frequency. The device is powered by an external power source. Power and signal transmission to the secondary equipment is carried out via a three-wire communication line;
- VEPS-PB1-02 - converts the value of the flow rate and volume into a pulsed output electrical signal with a frequency proportional to the flow rate, in accordance with the individual calibration characteristic. The signal frequency is equal to the vortex frequency. The device is powered by an external power source. Power and signal transmission to the secondary equipment is carried out via a two-wire communication line;
- VEPS-PB1-03 - converts the flow value into a unified DC signal 4 - 20 mA (0 - 5 mA or 0 - 20 mA - by special order), proportional to the flow. The device is powered by an external power source. The signal is transmitted to the secondary equipment via a two-wire communication line. The minimum current of the output signal corresponds to the flow rate Qmin in m3 / h (Table 1);
- VEPS-PB1-04 - converts the value of the flow rate and volume into a pulsed output electrical signal, normalized per unit volume, with a frequency proportional to the flow rate. The device is powered by an external power source. Power and signal transmission to the secondary equipment is carried out via a three-wire communication line;
- VEPS-PB2-01 - converts the value of flow and volume into a pulsed output electrical signal, normalized per unit volume, with a frequency proportional to the flow. The device is powered by a built-in self-contained power source. The signal is transmitted to the secondary equipment via a two-wire communication line.
Controlled environment parameters:
- temperature range ........................................... 5 to 150 ° FROM;
- working overpressure .......................... no more than 1.6 MPa;
- ionic conductivity .......................................... not less than 5 × 10- 4 cm / m;
- kinematic viscosity .................................... no more than 1.5 × 10-6 m2 / s ;
The limits of permissible basic relative error when converting the flow rate and volume into output electrical signals:
- at Qt≤Q≤ Qmax ............................................ . ± 1.0%;
- with Qmin≤ Q <Qt ............................................ . ± 1.5%.
The limits of additional errors of modifications VEPS-PB1-01, VEPS-PB1-02, VEPS-PB1-03, VEPS-PB1-04, VEPS-PB2-01 from the influence of changes in the temperature of the measured medium ........... .0.05% / 10 ° С (from the calibration temperature 25 ° С).
Degree of protection in accordance with GOST 14254-96 - IP65
- Performance group for resistance to mechanical stress according to GOST R 52931-N1
- Mean time between failures, h, at least - 75,000
- Average life, year - 15
Terms of Use:
- ambient temperature t, ° С:
- for modification of VEPS-PB1-01, VEPS-PB1-02, VEPS-PB1-03, VEPS-PB1-04 - from - 30 to + 50;
- for modification of VEPS-PB2-01 - from -10 to +50;
- relative humidity at t = +35 ° С and lower temperatures, without moisture condensation,% - up to 95;
- atmospheric pressure, kPa - from 84 to 106.7.
Intertesting interval - 4 years.
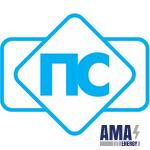