BPG gas Treatment units
Gas treatment units and complete gas treatment equipment included in them (OPGK) are designed to prepare gas entering the inlet (free (associated) oil, natural, fuel, impulse, buffer and other types of gas) to the required requirements of the Customer.
Gas preparation includes: purification of gas or other working medium from mechanical impurities and moisture, heating, distribution, accounting for the flow of the working medium, reducing and maintaining a given outlet pressure with a given accuracy.
BPG and OPGC can be placed in several separate block - boxes, in a single block - building of block - modular type, capital buildings and on open frames or frames with canopies.
BPG and OPGC are located and operated in open areas with seismicity of no more than 8 points according to SP 14.13330.2018.
By special order, BPG and OPGC can be designed and manufactured in seismic design for operation in areas with seismicity of 9 or more points.
BPG and OPGC can be used in the following climatic versions according to GOST 15150: "U"; "UHL".
Table 1 - GPG categories for explosion and fire hazard and the class of explosive zones
Name of premises and buildings | Explosion and fire hazard category according to NPB105-03 | Class of explosive zones according to PUE |
Rooms (block-boxes) for switching, cleaning, heating, reducing, accounting for gas consumption and other technological rooms | BUT | B-Ia |
Premises (block-boxes) of the control room, instrumentation, switchboard | B3 or B4 (depending on fire load) | Not standardized |
Premises (block-boxes) of coolant preparation units | G | Not standardized |
Under a separate agreement with the Customer, GPG can be designed and manufactured in other climatic modifications in accordance with GOST 15150-69, for a large load and have a different degree of fire resistance.
The designations of the basic versions of BPG and OPGC are given in Table 2.
Table 2. Basic version of BPG
Designation of a set of CD BPG | Productivity, m 3 / h (under standard conditions) | Gas pressure at the BPG inlet, MPa | Nominal diameter of the pipeline at the inlet of the GPG, mm |
one | 2 | 3 | four |
BPG Bunter-M.001.(12…160).03.X.X.2 | 1000 | 1.2-16 | fifty |
BPG Bunter-M.001.(16…160).06.X.X.2 | 1.6-16 | 32 | |
BPG Bunter-M.001.(25…160).12.X.X.2 | 2.5-16 | 25 | |
BPG Bunter-M.002.(12…160).03.X.X.2 | 2000 | 1.2-16 | 80 |
BPG Bunter-M.002.(16…160).06.X.X.2 | 1.6-16 | fifty | |
BPG Bunter-M.002.(25…160).12.X.X.2 | 2.5-16 | fifty | |
BPG Bunter-M.002.(12…160).03.X.X.2 | 3000 | 1.2-16 | 80 |
BPG Bunter-M.002.(16…160).06.X.X.2 | 1.6-16 | 80 | |
BPG Bunter-M.002.(25…160).12.X.X.2 | 2.5-16 | fifty | |
BPG Bunter-M.005.(12…160).03.X.X.2 | 5000 | 1.2-16 | 80 |
BPG Bunter-M.005.(16…160).06.X.X.2 | 1.6-16 | 80 | |
BPG Bunter-M.005.(25…160).12.X.X.2 | 2.5-16 | 80 | |
BPG Bunter-M.010.(12…160).03.X.X.2 | 10000 | 1.2-16 | 150 |
BPG Bunter-M.010.(16…160).06.X.X.2 | 1.6-16 | 100 | |
BPG Bunter-M.010.(25…160).12.X.X.2 | 2.5-16 | 80 | |
BPG Bunter-M.015.(12…160).03.X.X.2 | 15000 | 1.2-16 | 150 |
BPG Bunter-M.015.(16…160).06.X.X.2 | 1.6-16 | 150 | |
BPG Bunter-M.015.(25…160).12.X.X.2 | 2.5-16 | 100 | |
BPG Bunter-M.020.(12…160).03.X.X.2 | 20000 | 1.2-16 | 200 |
BPG Bunter-M.020.(16…160).06.X.X.2 | 1.6-16 | 150 | |
BPG Bunter-M.020.(25…160).12.X.X.2 | 2.5-16 | 150 | |
BPG Bunter-M.030.(12…160).03.X.X.2 | 30000 | 1.2-16 | 200 |
BPG Bunter-M.030.(16…160).06.X.X.2 | 1.6-16 | 200 | |
BPG Bunter-M.030.(25…160).12.X.X.2 | 2.5-16 | 150 | |
BPG Bunter-M.040.(12…160).03.X.X.2 | 40000 | 1.2-16 | 250 |
BPG Bunter-M.040.(16…160).06.X.X.2 | 1.6-16 | 200 | |
BPG Bunter-M.040.(25…160).12.X.X.2 | 2.5-16 | 200 | |
BPG Bunter-M.050.(12…160).03.X.X.2 | 50000 | 1.2-16 | 250 |
BPG Bunter-M.050.(16…160).06.X.X.2 | 1.6-16 | 250 | |
BPG Bunter-M.050.(25…160).12.X.X.2 | 2.5-16 | 200 | |
BPG Bunter-M.100.(12…160).03.X.X.2 | 100000 | 1.2-16 | 400 |
BPG Bunter-M.100.(16…160).06.X.X.2 | 1.6-16 | 300 | |
BPG Bunter-M.100.(25…160).12.X.X.2 | 2.5-16 | 250 | |
BPG Bunter-M.200.(12…160).03.X.X.2 | 200000 | 1.2-16 | 500 |
BPG Bunter-M.200.(16…160).06.X.X.2 | 1.6-16 | 500 | |
BPG Bunter-M.200.(25…160).12.X.X.2 | 2.5-16 | 400 | |
BPG Bunter-M.300.(12…160).03.X.X.2 | 300000 | 1.2-16 | 600 |
BPG Bunter-M.300.(16…160).06.X.X.2 | 1.6-16 | 600 | |
BPG Bunter-M.300.(25…160).12.X.X.2 | 2.5-16 | 500 | |
BPG Bunter-M.400.(12…160).03.X.X.2 | 400000 | 1.2-16 | 700 |
BPG Bunter-M.400.(16…160).06.X.X.2 | 1.6-16 | 600 | |
BPG Bunter-M.400.(25…160).12.X.X.2 | 2.5-16 | 500 | |
BPG Bunter-M.500.(12…160).03.X.X.2 | 500000 | 1.2-16 | 800 |
BPG Bunter-M.500.(16…160).06.X.X.2 | 1.6-16 | 700 | |
BPG Bunter-M.500.(25…160).12.X.X.2 | 2.5-16 | 600 |
On the whole, BPG are monoblock, or consisting of several block boxes, installations of full factory readiness with all necessary life support systems, which include fully assembled and tested equipment, which ensures accelerated installation of the product at the site of operation. The BPG block building is delivered to the construction site in the form of a separate shipping mark. At the installation site, the BPG block-building is installed on a pre-prepared foundation, which is carried out by the General Designer. The sizes of block-boxes have the ability to be transported by rail, water, and road transport at any distance.
The design of the BPG ensures operation without the need for constant and continuous monitoring by specialists in an automated mode.
The design, as well as the number of block-boxes or base frames that make up the object, depends on the design features and requirements of the Customer, specified in the questionnaire.
Depending on the purpose of the BPG, it may include:
1) knots:
- cleaning;
- prevention of hydrate formation and heating;
- pressure reduction (reduction);
- metering of gas consumption or other working medium;
- selection and preparation of gas for own needs;
- preparation of impulse gas;
- preparation of the coolant;
- distribution of gas or other working medium.
2) systems:
- automatic control;
- power supply;
- communications;
- protection against corrosion;
- heating and ventilation;
- gas contamination control;
- lightning protection and grounding;
- emergency, fire and security alarms;
- automatic fire extinguishing;
3) technological equipment:
- shut-off and safety fittings;
- gas pressure regulators;
- regulators - gas flow limiters;
- tanks for collection of gas cleaning products;
- containers for storing odorant;
- high pressure vessels;
4) technological pipelines;
5) primary means of fire extinguishing.
By agreement with the Customer, individual components and systems may not be part of the GPG or others may be included.
It is also possible to supply individual units (UOG, URG, UPG, etc.).
BPG (OPGK) meet the reliability requirements for safe operation with the following parameter values in accordance with GOST 27.002:
mean time to failure, h, not less than 15000;
average service life, years, not less than 33;
average recovery time
without taking into account the time of preparation for repair work., h, no more than 8.
Other values of the BPG (OPGK) parameters are possible upon agreement or requirements of the Customer.
Gas treatment units and complete gas treatment equipment included in them are manufactured in accordance with TU 28.99.39-005-91899331-2019.
The product design process is carried out by our own design department, whose specialists have many years of experience in designing oil and gas equipment of any complexity.
The production of equipment is carried out in Yekaterinburg at the own production site of United Oil and Gas Group LLC.
The production facilities include: production workshops, painting area, shot blasting chamber, plasma cutting, metalworking equipment, pipe bender, own non-destructive testing laboratory with all necessary equipment. about the same temperature sensor.
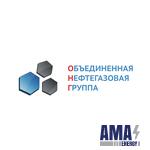