Oil and gas Separators NGS
Separation takes place in a special device called a separator. The importance of this device in the technological process is difficult to overestimate. Separators are widely used in many technological processes in the oil and gas industry:
- in fields for separating well products into gas, oil, and formation water;
- low-temperature separators for gas-fired units in gas treatment plants at fields and processing plants;
- at pyrolysis, catalytic reforming, isomerization, hydrotreating, catalytic cracking, etc. units at oil refineries;
- as part of flare installations (Order No. 779 of Rostekhnadzor “On approval of the Safety Guide for Flare Systems”);
- in gas preparation units at compressor stations – separators and plug catchers, etc.
Separators produced by the Neftegazoborudovaniye plant are divided into the following according to their shape and position in space:
- cylindrical horizontal
Advantages: easy to transport; easy to install on site; smaller diameter than a vertical separator with the same performance; lower cost of the device.
Disadvantages: more difficult to control the liquid level than in vertical separators; cleaning the apparatus from sand, dirt and paraffins is more difficult than in vertical separators; large liquid surface.
It is possible to equip horizontal separators with various internal devices: flow equalizer, drain shelves, various baffle nozzles, separation elements, mesh filters, defoamer, organization of separate liquid and gas input, heating coils depending on the purpose of the separator, the required parameters of liquid and gas at the outlet. Separators can be made of two sections: the upper - separation and the lower - for collecting liquid.
- cylindrical vertical
Advantages: complete capture of large quantities of mechanical impurities from gas; ease of cleaning the device from dirt; ease of monitoring the liquid level in the device; low evaporation of liquid.
Disadvantages: more difficult to transport and install; larger diameter than a horizontal separator with the same performance; high cost.
It is possible to equip vertical separators with various internal devices: a gas-liquid flow distributor, various baffle nozzles, separation elements, mesh filters, coalescing elements, coils for heating the liquid collection section, depending on the purpose of the separator, the required parameters of the liquid and gas at the outlet.
The operation of any separator is based on the application of one or several sedimentation principles; according to the sedimentation principle, separators are divided into:
- Gravity – separation occurs due to gravity. In such a device, the trajectory of liquid drops resembles the trajectory of a bullet. These separators are the most bulky and metal-intensive.
- Inertial – separation occurs under the influence of inertial forces that arise when the direction of the gas flow changes abruptly. This type of separators includes separators with baffle elements.
- Centrifugal – separation occurs under the action of centrifugal force. This type of separators includes separators with centrifugal-vortex nozzles, cyclones, and rotor-type separators.
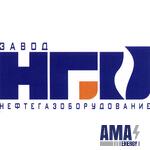