Welding unit UET-1
# | Parameter name | Equipment |
1. | VEHICLE | |
1.1. | Basic chassis | TSN-4 |
1.2. | Maximum transport speed, km/h (not more than) | 20 |
1.3. | Operating power of diesel engine with direct starter start of YaMZ brand, kW (hp) | 132 (180) |
1.4. | Specific fuel consumption in operating power mode, g/(kW/h) (g/(hp/h)) | 235 (173) |
1.5. | Caterpillar: | |
– number of links in one track, pcs. | 74 | |
– track link pitch, mm | 150 | |
– track link width, mm | 500-600 | |
– lug height, mm | 51 | |
1.6. | Number of gears: | |
- forward gear | 5 | |
- reverse | 1 | |
1.7. | Forward speed, km/h | 2-22 |
1.8. | Reverse speed, km/h | 4 |
1.9. | Base (distance between the axles of the outer support rollers), mm | 2880 ±10 |
1.10. | Track width, mm | 2050 ±20 |
1.11. | Ground clearance, mm | 537 ±10 |
1.12. | Maximum fordable depth, m | 0.8 |
1.13. | Maximum permissible tilt angle during movement, rad (degree) | |
- in the longitudinal direction | 0.44 (25) | |
- in the transverse direction | 0.34 (20) | |
1.14. | Maximum fuel tank capacity, l | 200 |
2. | MANIPULATOR | |
2.1. | Drive type | hydraulic |
2.2. | Load moment, tm | 4.0-7.1 |
2.3. | Maximum (minimum) reach of the manipulator, m | 5.5-7.3 (3.0) |
2.4. | Load capacity of the manipulator at maximum (minimum) reach, kg (not more) | 750-1000 (1330-2330) |
2.5. | Manipulator rotation angle in the horizontal plane, ° (not less than) | 315-400 |
3. | VAN (KUNG) | |
3.1. | Type | reinforced metal frame |
3.2. | Internal dimensions, mm | according to technical specifications |
4. | ELECTRIC UNIT | |
4.1. | Type and designation | Diesel AD100S-T400-1R |
4.2. | Engine, model | YaMZ-238M2 |
4.3. | Generator brand | Bokuk BK-150, Leroy Somer, BG-100 |
4.4. | Nominal power of generated electricity, kW | 100 |
4.5. | Type of current | variable |
4.6. | Nominal voltage, V | 400 |
4.7. | Nominal frequency, Hz | 50 |
4.8. | Nominal power factor (with inductive load) | 0.8 |
4.9. | Specific fuel consumption, g/kW h (not more than) | 252 |
4.10. | Capacity of the fuel tank of the electric generator, l | 240 |
4.11. | Duration of continuous operation of the electric generator engine at rated power, h | 10 |
4.12. | Specific oil consumption for burning, g/kW h (not more than) | 1.25 |
4.13. | Lubrication system capacity, l | 30 |
4.14. | Minimum load permissible for a long time, kW | 12 |
4.15. | Duration of continuous operation of the power unit at rated power without refueling, h (not less than) | 10 |
4.16. | Location of the power unit in the van | across |
5. | WELDING EQUIPMENT | |
5.1. | Number of welding stations: | |
– manual arc welding, no more than (or) | 4 | |
- semi-automatic welding, no more | 4 | |
6. | AUXILIARY EQUIPMENT (at customer's choice) | |
6.1. | Electrode drying oven SShO 3.2.3.2.5/4.0. | 1 |
6.2. | Thermo-box for electrodes TP 6/130 | 4 |
6.3. | Ring burners for heating pipe joints up to 1420 mm | 1 |
6.4. | Bosch grinder | 4 |
6.5. | Contact thermometer TK-5 | 3 |
6.6. | Halogen small spotlight (2 pcs.) with tripod | 2 |
6.7. | Sacit type welding mask | 4 |
6.8. | Assembly tent | 1 |
7. | Overall dimensions of the unit (LxWxH), mm (no more than) | 8550x2860x3950 |
8. | Total weight of the installation, t (not more than) | 19.5 |
Tractor chassis TSN-4 . Using a skidding machine widely known in the Russian Federation as a base chassis allowed us to create a welding unit with high cross-country ability for use in highway conditions.
The van is insulated with a frame structure , the outside is made of welded corrugated steel sheet, the inside is lined with non-combustible material, the walls are insulated.
The van has several compartments and contains the following equipment:
The 100 kW electric unit is installed in a separate unit compartment with the radiator close to the wall, in which an outlet window for cooling is made. Exhaust gases are discharged through the muffler.
Welding sources (4 posts) are installed in the main compartment of the van. Welding units UET-1 (AST) are equipped (up to 4 posts) with modern welding equipment from Lincoln Electric (USA), which allows combining various types of welding (automated wire welding, various methods of semi-automatic welding, stick electrode welding) into a single technological process.
Remote equipment , in particular LN-23P/LN-27 wire feed units, welding cables and grounding cables, pipe cutters, cutting torches with hoses, windings for demagnetizing pipe joints, spotlights, remote controls with cables, etc. are stored in separate compartments with access from outside the van. When working with remote equipment at a distance of up to 30 m, the passage of cables and hoses from the compartments is ensured with the doors closed.
The crane-manipulator unit (KMU) for carrying out cargo handling operations is mounted on the vehicle chassis between the cabin and the van. It has mechanized movement in the horizontal and vertical planes. Usually, a hydraulic manipulator with a lifting capacity of 750-1000 kg at a reach of 5.5-7.1 m with a hook suspension is used as a KMU . The hydraulic system of the manipulator is activated from the hydraulic system of the tractor. The manipulator is controlled from the tractor cabin. The axis of horizontal rotation of the manipulator coincides with the longitudinal plane of the chassis. In the transport position, the manipulator rests on the front pillar in front of the cabin. At the customer's request, other types of manipulators and a different arrangement on the chassis can be used.
The welding tent or shelter in a folded state is placed on the roof of the van, where access is provided from the ground and the crane suspension of the KMU.
High-pressure cylinders are installed in an open area, where the crane suspension of the KMU is accessible, or there is the possibility of installing and replacing them manually.
At the customer’s request, it is possible to place equipment required for work on main pipelines, as well as other welding equipment.
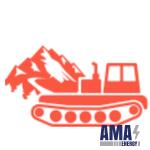