ULTRA-CUT® XT Systems plasma cutter
Superior cutting quality means greater efficiency
The Ultra-Cut XT delivers superior cutting quality, which means that workpieces can be transferred directly from the cutting table for welding, painting or assembly without costly secondary machining operations.
Ultra-Cut XT precision plasma cutting systems cut with:
Excellent quality, without scale using oxygen (O2) plasma on black steels.
Unsurpassed quality on non-ferrous metals using unique technology of cutting in a water fog (Water Mist Secondary WMS ®).
ISO 9013: 2002 (E). Grade 3 or better, really high-precision cutting (depending on thickness, edge angles are always below 3 degrees).
Minimum heat affected zone (HAZ).
3DPro technology sets a new standard in robotic thin metal cutting.
High performance for greater economic benefits.
Ultra-Cut XT XT precision cutting systems deliver superior cutting quality at high speeds.
The excellent consumable life reduces downtime for replacement and reduces cutting costs.
High power for maximum on-time and cutting speed.
Reduced downtime when changing consumables due to the quick-release design of the Speedlok cartridge.
Low current consumption reduces costs.
Reduce switching time between marking and cutting for greater utilization.
The highest cutting speed of stainless steels and aluminum in this class is up to 3 times faster than similar cutting systems.
Reduces your energy bills
Compared to previous systems, Ultra-Cut XT systems consume approximately 20% less current and have an electrical efficiency greater than 92%. They comply with European Union Level V performance standards and help companies worldwide reduce energy costs.
Intelligent solutions highlight
Compared to previous systems, Ultra-Cut XT systems consume approximately 20% less current and have an electrical efficiency greater than 92%. They comply with European Union Level V performance standards and help companies worldwide reduce energy costs.
Us Victor® Thermal Dymanics® offers intelligent, high-precision solutions for automatic plasma cutting applications, from superior thick metal cutting technology to high-quality marking. The XT Series provides access to these powerful cutting resources.
HeavyCut ™ Technology
To ensure better cut quality, consumable life, and cutting accuracy, rely on HeavyCut technology using XTremeLife ™ consumables when cutting parts thicker than 20 mm. HeavyCut 300 A and 400 A electrodes, with several hafnium inserts, have an unrivaled resource when cutting at high currents.
Diameter PRO ™ Technology
ULTRA-CUT tab4.pngDiameter PRO is an intelligent software-based solution that allows Victor Thermal Dymanics iCNC XT to optimize hole quality in parts with a ratio of thickness to cut diameter of 1: 1 or more. This is an ideal process for cutting precise holes or radii, with a minimum taper of the edge or no taper at all in mild steel from 3 to 50 mm thick or in aluminum up to 25 mm thick.
Cutting in water mist (Water Mist Secondary - WMS), optimal for stainless steel and aluminum
The WMS process provides excellent cutting quality and low maintenance by using nitrogen and water vapor as a protective medium as a plasma gas. Due to the formation of hydrogen from water vapor during cutting, a reducing atmosphere is created and this atmosphere reduces oxidation on the surface of the cut. WMS is recommended for materials up to 40 mm thick.
The fastest non-ferrous metal cutting process. Cuts at speeds significantly higher than cutting with H35 (Ar / H2)
Excellent cutting quality using N2 as a plasma gas and water as a protective environment.
Lowest operating costs.
Slag-free cutting of parts with a thickness of 1 mm to 40 mm.
Cut surface without oxides.
ULTRA-CUT tab5.pngWide setting range of possible cutting parameters
Additional flexibility in use - the ability to increase power with the growth of your needs
The design of the systems allows them to grow with your business. You can start with the Ultra-Cut 100 XT, and when you are ready, you can increase the power to 200, 300 or 400 Amps. With Ultra-Cut XT, you never have to worry about choosing the right system and buying the system “with a margin."
Victor Thermal Dynamics has developed Ultra-Cut XT with the ability to increase the power of the current source in accordance with the growing needs of your production. The system has a modular design consisting of a set of “Inverter Blocks”. To increase power from 100A to 200A, 300A or 400A, simply install additional units *. An ordinary technician can install a new unit in less than 30 minutes.
The unique approach of Victor Thermal Dynamics is that you do not have to buy equipment again. With Ultra-Cut XT, you will always have the right amount of power today and tomorrow, depending on your needs.
* If you increase to 200 Amperes or more, connect the necessary additional external cooler to the system, install the correct consumables and you are ready for cutting.
Ease of Maintenance
The modular design of Ultra-Cut XT systems makes it not only easier to upgrade the system, but also easier to maintain.
Error / Current Monitor displays the status of the XT system and speeds up troubleshooting
Minimize inventory with versatile components for the entire XT ULTRA-CUT line
Optimal Gas Management and Plasma Marking with Automatic Control
Optimizing gas flow improves cutting quality and extends the life of consumables. Digital flow control with automatic pressure control can also be performed with ICNC XT CNC, providing a higher level of cutting quality control. Working together, Ultra-Cut XT and ICNC XT instantly set the right gases and adjust their pressure, achieving faster cycle times and faster cutting.
With plasma argon marking, the Ultra-Cut XT automatic gas console minimizes the purge cycle between marking and cutting, and also eliminates the time required for manual reconfiguration. Fast automatic switching between cutting and marking:
• Marking of part numbers • Marking of the center of the holes • Places for welding parts • Lot numbers • Bending lines or pieces
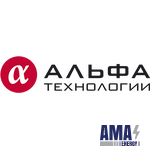